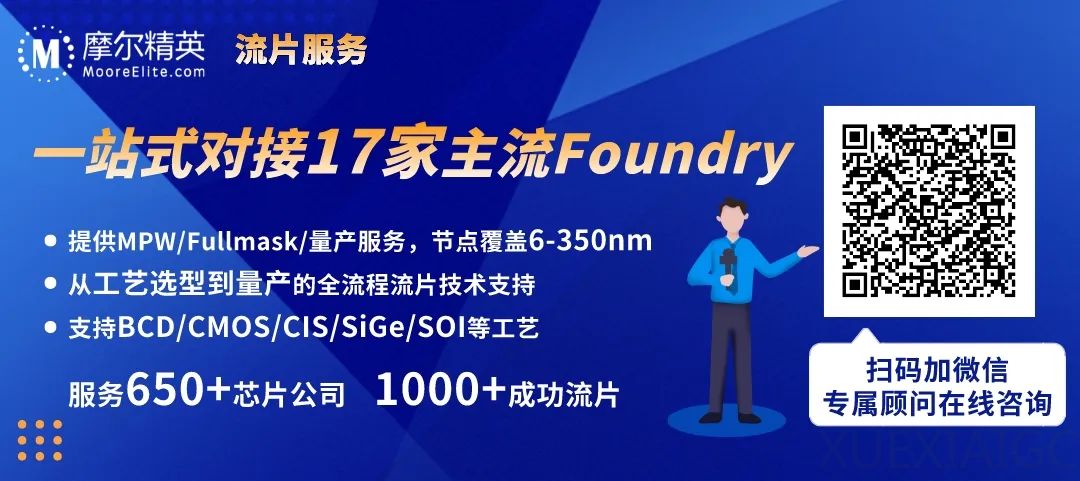
文章摘要
【关 键 词】 硅通孔、3D封装、芯片互连、背面供电、技术挑战
硅通孔(TSV)技术在2.5D和3D封装中扮演着关键角色,通过缩短互连长度来降低芯片功耗和延迟,从而加快信号传输速度。TSV技术最初用于CMOS图像传感器,现在已扩展到支持MEMS、RF系统和逻辑器件背面电源方法的集成。TSV的尺寸因应用而异,从CMOS图像传感器的几十到几百微米,到硅中介层的几十微米,再到背面电源传输的5nm以下。
尽管TSV技术已有数十年历史,但其高成本限制了广泛应用。随着通孔变得更窄更深,制造成本增加,因为需要更长的时间来蚀刻更深的沟槽,更难沉积连续衬垫和阻挡金属,且镀铜过程必须更精确以确保可靠连接。设备和材料供应商正致力于生产一致、可靠的TSV,同时降低成本。
TSV对周围区域施加的机械应力和热应力是一个关键考虑因素。通孔的纵横比越大,制造工艺对周围硅片产生的拉伸应力就越大,这会影响载流子迁移率和晶体管开关速度。工程师们正在探讨TSV邻近效应,以最小化缓冲区的大小。
TSV的制造涉及五个工艺步骤:光刻图案化定义沟槽特征、反应离子蚀刻(RIE)创建沟槽、沉积SiO2衬垫、共形沉积阻挡金属、电化学沉积(ECD)填充铜,最后化学机械平坦化(CMP)抛光铜覆盖层。TSV中可以使用除铜以外的其他导体,如多晶硅填充用于MEMS,钨填充用于背面电力传输连接。
TSV流程可以在制造任何有源器件之前插入,称为先通孔处理,也可以在前端器件存在之后但在形成接触和金属互连之前进行中间通孔,或在部分或全部后端互连到位之后进行后通孔。
随着TSV尺寸越来越小,薄阻挡层金属仍需要提供保形沉积,尽管ALD被视为一种替代方案,但批量生产中的低产量使工艺流程中保留了更成熟的沉积工具。电镀平台供应商寻求快速填充TSV沟槽,并实现晶圆与晶圆之间的一致性,这需要工具制造商和材料供应商密切合作,开发专用TSV电镀化学品。
TSV技术可实现芯片间的高密度垂直互连,显著减小终端设备的三维尺寸,降低设备的功耗、提高数据传播速度并提高系统的可靠性。TSV流程还需要与后续焊料凸块、微凸块或混合键合互连紧密集成,机械和电气因素都会发挥作用。
背面供电是三大代工厂为2nm节点器件开发的一种新方法,通过在先进逻辑芯片中使用大约15层铜互连将电源与信号线隔离,背面配电可通过降低电压下降和RC延迟将功率损耗降低高达30%。背面供电有三种方法,每种方法的工艺复杂程度都在不断提高,但都具有更好的扩展性和性能优势。
小芯片概念的出现和3D集成应用的不断增长引起了人们对硅通孔技术的极大关注。随着互连集成密度的不断提高,具有小临界尺寸(CD)和高纵横比(AR)的TSV的金属填充变得越来越具有挑战性和成本。因此,越来越多的趋势是研究高质量和低成本的方法来创建和填充更小、更深的TSV,同时确保与其他芯片的出色连接。工具制造商和材料供应商将继续开发用于互连3D封装并最终用于3D-IC的下一代TSV解决方案。
原文和模型
【原文链接】 阅读原文 [ 3604字 | 15分钟 ]
【原文作者】 半导体行业观察
【摘要模型】 moonshot-v1-32k
【摘要评分】 ★★★★★