150PB工业数据+智能体革命,西门子开启AI制造新纪元
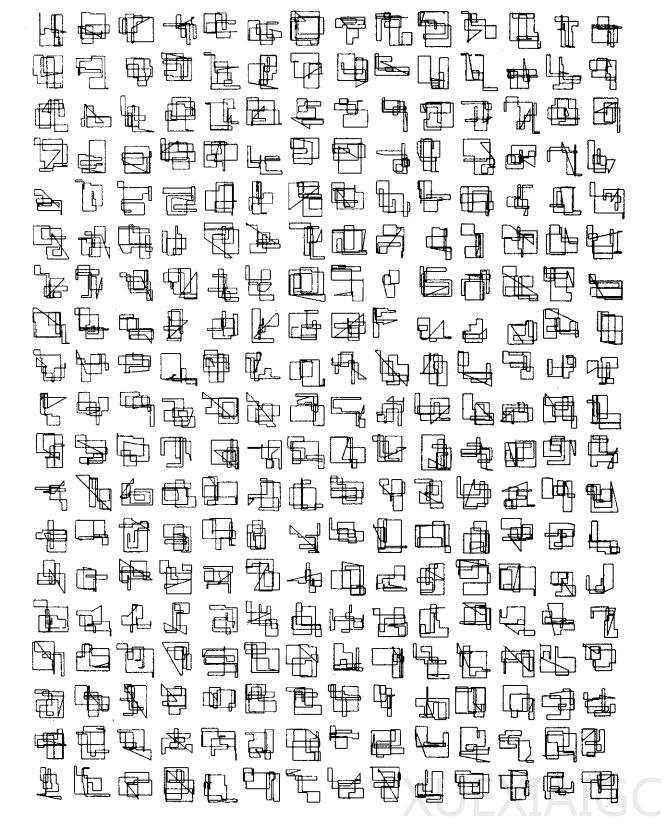
文章摘要
【关 键 词】 计算机艺术、工业AI、智能制造、数字孪生、算法生成
1964年德国爱尔兰根的西门子数据中心,一台Zuse Graphomat Z64绘图仪在数学家Georg Nees的指令下,诞生了世界上首批计算机生成图像。这场发生在工业环境中的艺术实验,意外开启了人工智能与制造业融合的序章。六十年后,这座小城已成为西门子”全球灯塔工厂”的所在地,超100项AI应用深度嵌入制造流程,数字孪生技术构建起虚实交融的生产镜像。
工业智能体系统正重塑人机协作范式。荣获”工业界奥斯卡”的Industrial Copilot不仅能理解自然语言指令,更能将之转化为150行可执行的自动化代码,使开发效率提升50%,代码部署时间缩短30%。其核心在于由”指挥家”(Orchestrator)智能体协调的分布式系统,能够根据标准作业流程拆解任务,联动设备状态监测、产线参数调整、物料核算等子模块完成复杂操作。当操作者要求”新增订单并提前三天交付”时,系统会自主规划从生产排程到AGV运输的全链条响应。
支撑这一体系的工业基础模型(IFM)展现出与消费级AI的本质差异。由150PB工业数据浇灌的模型群,包含擅长时间序列分析的GTT模型、精通PLC编程的专用模型等,形成能理解机器语言的多模态认知体系。这些模型严格遵循工程语义和工业逻辑,对图纸几何结构、控制流程图、传感器脉冲等专业数据具有独特解析能力。与通用大模型不同,小数点级的精度偏差就会触发IFM的修正机制,这种严苛的容错标准源于西门子百年积累的工程经验。
数据资产与行业know-how构成难以逾越的壁垒。西门子覆盖全球40万客户的软硬件生态,形成了从CAD设计到PLC控制的完整数据闭环,仅时间序列模型训练数据就达1240亿条。在数据采集环节,毫秒级实时监测与小时级周期采集的混合方案,需要深度理解不同工艺特性;在模型部署阶段,Modbus、OPC UA等异构协议的兼容转换考验系统级适配能力。更关键的是持续运维机制——当传感器漂移导致模型失效时,工厂工程师可通过点击界面自主完成模型再训练。
这种能力积淀源自1973年西门子获得的首项AI专利,历经神经网络控制系统的早期探索,直至今日1500名专家构建的研究体系。近期收购Altair和Dotmatics的战略动作,将AI触角延伸至仿真优化和生命科学领域。在WAIC 2025中国首秀中,Industrial Copilot将展示其驱动AGV、机械臂协同作业的实时决策能力,继续书写计算机艺术发源地的新篇章——那里,算法正从自动化走向自主化,重新定义制造的底层语法。
原文和模型
【原文链接】 阅读原文 [ 4198字 | 17分钟 ]
【原文作者】 机器之心
【摘要模型】 deepseek/deepseek-v3-0324
【摘要评分】 ★★★★★